Какие изменения ожидают фарму в будущем?
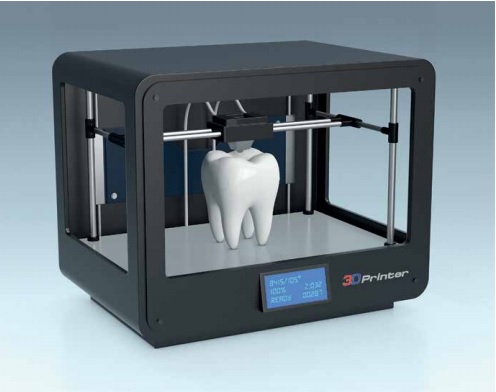
Несколько лет назад «гуру» на учной фантастики, писатель Айзек Азимов жаловался, что многие из его «фантастических» романов угодили на полки библиотек в раздел «наука». Двигаясь спринтерскими темпами, наука обогнала самые причудливые
идеи фантаста. Аналогично многое из того, что я рассматриваю как «будущие» усовершенствования, уже внедрено на ряде предприятий. Тем не менее для большинства практиков они все еще могут быть тайной или, по крайней мере, слухами.
Поскольку FDA США вдохновляет фарму наконец войти в XXI век (часть названия Руководства), ряд прогрессивно мыслящих крупных компаний, как говорится, поймали данную организацию на слове. Однако инерция в фармацевтической отрасли намного более выражена, чем в других отраслях промышленности. И это естественно, учитывая, что FDA было создано с единственной целью – прекратить эксплуатацию с нарушением правил и отклонений от нормы в фармацевтической отрасли или, другими словами, выполнять функцию полицейского. За период с момента создания данного ведомства силу закона приобрели многие сложные «драконовские» правила. На вопрос «Как следует написать тот или иной раздел документа (NDA или ANDA)?» наиболее распространенным ответом было «Дайте нам что-то – и мы скажем, годится оно или нет».
С целью обезопасить себя фармацевтические компании просто выбирают самый консервативный сценарий, а именно:
1. Каждый пакет подаваемых документов должен быть таким же, как последние 200. («Если это работало в течение последних 60 лет, то зачем подставляться?»)
2. Используют самые прогрессивные технологии и методы (NMR, Raman, LC-LC, LC-MS и т. д.), чтобы максимально гарантировать безопасность и активность АФИ, а затем просто применять методы «мокрого» анализа для исследования готовых препаратов по Американской или Британской Фармакопее. Тем самым обеспечивается регистрация по ускоренной процедуре (и максимально сохраняется патентная защита), поскольку не требуется проведение дополнительной валидации.
3. Поскольку для внедрения любой «новой» концепции или технологии / проведения мониторинга производства нужна всесторонняя (читай: времязатратная и дорогая) валидация, производители используют подходы к разработке и производству, которые применялись в 50-х годах прошлого столетия.
4. Учитывая, что производство в XXI веке – это просто укрупненная версия производства середины 50-х годов прошлого столетия, минимум тестирования считается «более безопасным», чем проведение большего количества тестов.
Четвертый пункт, по сути, является основной причиной сопротивления, оказываемого внедрению процессно-аналитической технологии (РАТ), а именно: если мы слишком много тестируем, то найдем проблемы в каждой партии. Это вполне справедливое утверждение, поскольку в пределах каждой партии отклонения таких показателей, как содержание активного вещества, твердость, масса и т. д., характеризуются кривой Гаусса. Поэтому, если это не процесс «шесть сигм», то при выпуске партии объемом несколько миллионов единиц количество продукции с отклонениями может исчисляться сотнями и даже тысячами. Это происходит в рамках парадигмы традиционного производства «сначала сделай – затем проверь». Если РАТ используют только для того, чтобы провести анализ устаревшего способа производства, то в результате можно обнаружить все слабые места и отклонения. Можно (или следует) использовать PAT и качество, встроенное на этапе разработки (QbD), для ускорения выпуска и повышения качества продукции?
От современного РАТ до QbD
Хотя самой идее РАТ уже лет 15 или даже больше, внедрение программы РАТ представляется все еще целесообразным. Предположим, что компания осуществила большие инвестиции в традиционное производство продукции партиями. В этом случае внедрение РАТ может быть полезным в таких аспектах:
- Первая часть PAT / QbD, которую часто пропускают, касается проведения качественного анализа входящего сырья (вспомогательные вещества и АФИ). Я также рекомендую проведение 100 % проверки во избежание пропуска контейнеров без этикеток или содержащих испорченный продукт (часто используемое выборочное тестирование по принципу √n + 1 приводит к тому, что из 100 контейнеров проверяют только 11, тогда как в оставшихся 89 потенциально могут скрываться ошибки).
- Измеренные параметры сырья помогут оператору правильно оценить время смешивания, которое, например, для материалов, содержащих более мелкие частицы, меньше, чем для материалов с более крупными частицами.
- Даже если все партии входящего сырья окажутся приемлемыми, экономия времени на квалификацию в режиме реального времени (например, 1 час на проверку 200 мешков лактозы по сравнению с 1 неделей в лаборатории контроля качества) стóит времени и денег, затраченных на проведение валидации программы. (И это без учета этикетирования входного материала как «тестируемого», его нахождения на карантине, повторного этикетирования на прошедшее проверку или отправленное на уничтожение, перемещение его в разные участки складского помещения. При проведении же 100 % проверки сырье можно или немедленно использовать, или отправить поставщику на доставившем его грузовике).
- Cобранную на этапе входящей квалификации информацию о физических параметрах затем передают в отдел R&D на пилотное или промышленное производство для планирования операций смешивания и т. д.
- Следующий, самый простой этап в программе РАТ – установка встроенного в линию датчика, проверяющего однородность смеси в режиме реального времени, что позволяет определять оптимальное время смешивания. Довольно часто смешивание продолжается дольше, чем это необходимо, просто, чтобы «быть уверенным». И так год за годом. Определение оптимального времени смешивания поможет сэкономить несколько минут на производстве каждой партии, что в результате даст вам дополнительные мощности без каких-либо дополнительных затрат. (В результате смешивания образуется тепло, которое, в свою очередь, приводит к деградации материала, изменению его полиморфизма или просто к измельчению частиц).
- Кроме этого, наличие активного мониторинга на каждом производственном участке способствует выполнению требований GMP в отношении «наличия встроенного в процесс достоверного тестирования». Полученные таким образом данные будут не только достоверными, но и своевременными, что потенциально поможет избежать ошибок.
- Еще одно часто игнорируемое требование GMP касается «проведения тестирования статистически значимого количества готовых лекарственных форм». Понятно, что 10, 20 или даже 30 таблеток из партии объемом 3 – 5 млн единиц не являются «значимым количеством» ни в одном курсе статистики, который преподают во всем мире. Тестирование с использованием высокоскоростной жидкостной хроматографии (HPLC) не подпадает под определение ни своевременного, ни представительного, так как его невозможно провести для большого количества образцов из партии (вероятно, измеряемого тысячами?). Время и затраты – основные причины, по которым не анализируется большое количество образцов с использованием методов HPLC. Так что мы «wink-wink, nod-nod» («перемигнулись, покивали» – ред.) и уверовали в то, что правильно осуществляем выборку образцов для процесса производства. Использование встроенного в линию спектрометра позволяет как контролировать, так и получать картину «доброкачественности» производимой партии от начала и до конца.
- И заключительный комментарий: любой контрактный производитель, имеющий PAT/QbD, является более привлекательным для клиента, поскольку может произвести продукт быстрее и лучшего качества.
Продолжение статьи читайте на страницах журнала "Фармацевтическая отрасль" №5 (64), октябрь 2017 г.
30.10.2017